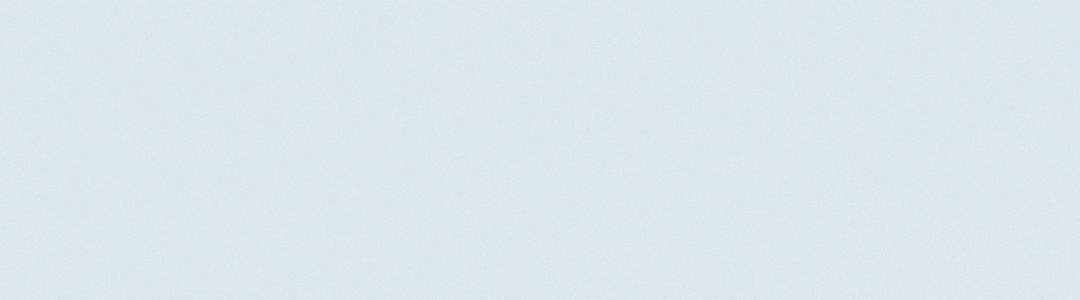
1. Metallurgy Crane Definition
Kingda metallurgy crane is a special use lifting equipment which is applied for handling molten metal in metal smelting workshop, crane bridges move along with workshop’s rail, hoist trolley travels along with crane’s main girders and the hook lifting-lowering by trolley’s drum.
For this article, it is the depiction for the definition, application, operating environment, characteristics and classification of metallurgy cranes equipped at ironmaking, steelmaking and continuous casting workshop for every process flow. Also simply discussed the requirements of cranes to all process flow at steel-making factory. There will be some guidance function for the type-selection and the design of cranes.
Metallurgical cranes include ferrous metallurgy crane, nonferrous metallurgy crane and hot working crane.
Ferrous metallurgy crane usually refer to specific cranes that complete specific work in production processes such as ironmaking, steelmaking, and rolling. Nonferrous metal cranes usually refer to special cranes specifically designed for smelting factories of non-ferrous metals (copper, lead, nickel, lead, zinc, etc.). Hot working crane usually refers to the special crane used in hot working (forging, heat treatment) workshop to change the pieces’ shape and material metallographic structure.
The special or specialized cranes mentioned above are collectively referred to as metallurgical cranes.
Kingda metallurgy crane working temperature: -10℃~60℃, humidity not exceeds 50%, molten metal’s radiation to gantry hook and forging hook not exceeds 300℃. crane’s working class/level can be A7, A8, used in heavy duty metallurgy, foundry and casting workshop.
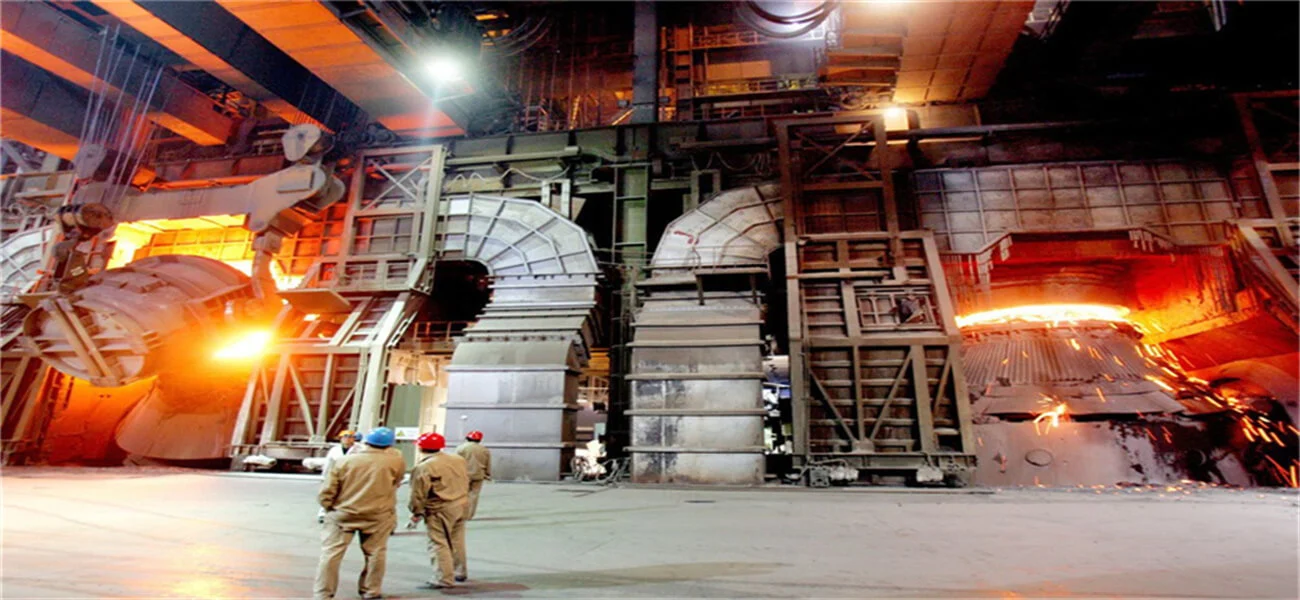
2. Metallurgy Crane Application
Kingda crane metallurgy crane mainly used for metal smelting (iron-making and steel-making), rolling process(hot rolling and cool rolling) and hot working, it is a special purpose crane. In metallurgy family, there are
Ferrous Metallurgy Crane |
Nonferrous Metallurgy Crane |
Hot Working Crane |
ladle crane/casting crane/foundry crane |
anode baking furnace multifunctional crane |
forging crane |
charging crane/feeding crane |
electrolytic aluminum multifunctional crane (PTM) |
quenching crane |
slab tong crane |
anode carbon block stacking crane (ASC) |
|
electromagnet suspension balancing beam crane |
electrolytic multifunctional copper crane |
|
coke dry quenching (CDQ) coke pot (Bucket/tank) handling crane |
|
|
3. Metallurgy Crane Operating condition
3.1 Environment
Metallurgy crane’s design, manufacturing should follow relevant technical standard and safety requirement.
3.1.1 Crane’s power source usually is 3 phase-50hz-380V(can be tailored by end user’s condition), voltage fluctuation to motor and electrical appliance is +10%,lower limit(peak current) is -15% of rated voltage; Inner voltage loose should not less than 5% for stripper crane and billet handling crane, to others crane should not less than 4%.
If there are special voltage requirements, can be tailored for customer’s condition.
3.1.2 crane’s installation and operating site’s elevation should not exceed 2000m(if exceed 1000m, should check motor’s capacity)
3.1.3 operating environment and temperature
A. Operating temperature:-10~+50℃;
B. Humidity not exceeds 50% under working temperature+40℃
3.1.4 In working site, should no inflammable, explosive and corrosive gas
4. Metallurgy Crane Characteristics
4.1 High working level
The utilization level and load state of the crane determine the Metallurgy crane’s working level.
The utilization level of a crane refers to the total number of cycles within its design life cycle, According to the crane design specification, depending on different cycling numbers, the crane is divided into U0-U9, total of 10 grades. Metallurgy cranes work very frequently, utilization level greater than U6.
Crane’s load state indicates the degree of load it is subjected to, which is related to two factors: the ratio of the lifted load to the rated load (Fi/Fmax); And the ratio of each lifting load Fi’s action number to the total number of cycles N (ni/N). The full load rate and number of full loads of metallurgical cranes are very high, load state is Q3 or Q4, therefore, crane’s working level is A6-A8.
4.2 Harsh working environment
Most metallurgy cranes work in harsh environments with high temperatures, high dust, and even harmful gases.
Therefore, metallurgical cranes should have protective measures such as heat insulation, dust prevention, and corrosion prevention.
5. Metallurgy Crane Technical Requirements
Crane’s designer should recognize that Metallurgy cranes are "special equipment that involves life safety and poses significant risks"
- Metallurgical cranes should be safe and reliable to avoid malignant accidents;
- Emphasize environmental protection and meet emission standards;
- The design and manufacturing of metallurgy cranes must comply with national standards and laws and regulations
6. Metallurgy Crane Developmenting Direction
6.1 Increase lifting capacity, increase travel speed, To adapt to high productivity
With the Iron and steel factories’ expansion of production scale, smelting and rolling are both developing towards large-scale production, encouraging the crane to increase its lifting capacity and all mechanism’s speed to meet the requirements of productivity.
6.2 Widely apply monitoring, Sensing control technology
Safety and reliability are paid for concentration, Various safety detection devices are widely used on cranes, the application of detection sensing control technology greatly improves the safety and reliability of cranes.
6.3 Promote and popularize speed control systems, reduce dynamic load and improve positioning performance
To improve productivity, cranes must operate at high speeds to reduce work time, providing precise positioning at low speeds to improve work efficiency. Only stable braking and fast operation can meet the above requirements, so equip each mechanism with a speed control system on the crane is the best way.
6.4 Programmed control technology, achieve full automation and semi-automation
Rapid development of control technology today, Providing conditions for crane’s automation and semi-automatic control.
6.5 comfortable operating environment, more convenient maintenance
“Focus on end user’s willingness, let all operator fells satisfied” It is the responsibility of every crane designer and manufacturer.
6.6 Standardization for structure and modularization
Structural optimization has now become a necessary step in the design process, on this basis, coordinating various products and designing them according to standardization, modularization, and generalization will bring significant
benefits.
6.7 Adopting an international production model
Continuously improving the technical level, expanding the international market, we need to align our production and supporting models with international standards, Adopting an international production model.
7. Metallurgy Crane Classification
7.1 Ferrous Metallurgy Crane
7.1.1 Ladle Crane/Casting Crane/Foundry Crane
7.1.1.1 Definition and usage
Special metallurgy crane used for lifting molten metal are collectively called as ladle crane (casting crane or foundry crane). The casting crane (casting crane or foundry crane) is mainly used for adding molten iron into the converter (BOF) in charging bay, Lifting the steel liquid to the refining furnace(LF) at the refining bay, Alternatively, the steel liquid can be lifted onto the continuous casting ladle turntable at the receiving bay, or lifting liquid steel to continuous casting ladle rotary table in liquid steel receiving bay. It is one of the key equipment in the steel-making and continuous casting process
7.1.1.2 Characteristic
Ladle crane lifts molten metal and work in high temperature and dust environments, high level of work, after a malfunction occurs, it may cause significant losses and serious consequences. Due to casting crane needs to complete the function of dumping molten metal and its slag, it should have at least a main hook and a Aux. hook.
7.1.2 Charging Crane/Feeding Crane
7.1.2.1 Definition and usage
In the steel-making workshop, a metallurgy crane for adding scrap steel and other auxiliary materials (cold materials) to a converter furnace (BOF) or electric furnace (EAF) is named feeding crane. The working load is the sum of the weight of the lifted feeding box and materials inside the feeding box
7.1.2.2 Type and Characteristic
There are two modern steel-making methods: electric furnace steel-making and converter steel-making, and different steel-making methods require different charging crane/feeding crane. The main raw material for converter steel-making is molten iron, adding cold materials during the steel-making process. The customized crane configured to complete the cold material addition operation is the feeding box charging crane/feeding crane.
The main raw material for electric furnace steel-making is scrap steel (molten iron or steel), the electric furnace feeding crane is mainly used to add scrap steel to the electric furnace. Its structure is similar to that of a casting crane, The main difference in design compared with casting/ladle crane is that the main lifting mechanism does not need to consider the single mechanism working condition.
7.1.3 Slab Tong Crane
7.1.3.1 Characteristic and usage
The slab tong crane is a specialized metallurgy crane for handling slabs, especially high-temperature slabs, used to transport high-temperature slabs on the continuous casting production line to the billet warehouse and heating furnace, Or transport slabs (room temperature) in the finished product warehouse, stack them, and load and unload from vehicles. It can lift slabs or blooms with a thickness of over 150mm, and the temperature can be above 650 ℃ when lifting high-temperature slabs.
The slab tong crane is a type of slab handling crane, usually the structure is double beams, double rails and single trolley. Its retrieval device is a specialized slab tong, The crossbeam on the double lifting point is connected to the trolley through a lifting wire rope system (or hook). Due to working on the main production line, the working level of the slab tong crane is relatively high, often A7, A8.
The lifting capacity of the slab tong crane refers to the effective lifting capacity of the slab held by the tong (net lifting capacity). Rated lifting capacity of the lifting mechanism=slab weight+tong weight (+guide cylinder weight).
.WEBP)
7.1.3.2 Type
The slab tong crane is classified according to its structure form and usage requirements; According to the types of suspended tongs, they are divided into electric slab tong cranes and automatic slab clamp (gravity clamp) cranes; According to the clamp suspending method, it can be divided into flexible slab tong crane, rigid slab tong crane, and rotary slab tong crane; The rotary slab tong crane is divided into the upper rotary slab tong crane and the lower rotary slab tong crane.
Various types of slab tong cranes, according to the position of the slab relative to the main beam, it can be divided into two types: slab tong verticals to main beam type and slab tong parallels to main beam type.
|
|
|
|
|
|
|
|
|
slab tong crane Category Summary |
|
|
|
|
|
|
|
|
|
|
|
|
|
|
|
|
|
|
|
|
|
|
|
|
|
|
|
|
|
|
|
|
|
|
|
|
|
|
|
|
|
|
|
|
|
|
|
|
|
|
|
|
|
|
|
|
|
|
|
|
|
|
|
|
|
|
|
|
|
|
|
|
|
|
|
|
|
tong driving mode |
|
|
|
suspend tong ways |
|
|
|
|
slab direction conversion |
|
|
|
|
slab's direction to main girder |
|
|
|
|
|
|
|
|
|
|
|
|
|
|
|
|
|
|
|
|
|
|
|
|
|
|
|
|
|
|
|
|
|
|
|
|
|
|
|
|
|
|
|
|
|
|
|
|
motor slab tong crane |
|
automatic slab tong crane |
|
flexible slab tong crane |
|
rigid slab tong crane |
|
upper rotary slab tong crane |
|
lower rotary slab tong crane |
|
slab tong verticals to main beam |
|
slab tong parallels to main beam |
7.1 4 Suspension Balancing Beam Crane with Magnet
7.1.4.1 Characteristic and usage
The suspension balancing beam crane with magnet is the main metallurgy crane for handling square billets, profiles, bar wires, medium- thick plates, rolling plates, thin plates, and pipes. It is mainly used for continuous casting, continuous rolling workshops, or finished product warehouses.
The suspension balancing beam crane with magnet is divided into two types: hook suspension balancing beam crane and electromagnet suspension balancing beam crane. This chapter mainly introduces electromagnet suspension balancing beam crane. The hook suspension balancing beam crane has the same structure as the electromagnet suspension balancing beam crane, except that the lifting device is a hook. The electromagnet suspension balancing beam crane is a double beam-single trolley Overhead crane. Its picking device is a special lifting electromagnet.
The double lifting point suspending beam is connected to the trolley's lifting wire rope system (or hook). The electromagnet suspension balancing beam crane is used to transport finished steel plates, billets, and sections from the roller track to the stacking platform in the production line of the continuous rolling workshop. Loading and unloading from vehicles or carrying out stacking operations in the finished product warehouse. The temperature of the steel and the slab is generally below 650 ℃. The electromagnet suspension balancing beam crane is mainly used on the main production line of the steel rolling plant and in the finished product warehouse, therefore the work level is higher, usually A7, A8.
.WEBP)
7.1.4.2 Type
Suspension balancing beam crane with magnet can be roughly divided into three categories according to different usage requirements, they are general electromagnetic suspension balancing beam crane, rotating electromagnet suspension balancing beam crane and special electromagnet suspension balancing beam crane. Among them, the rotating electromagnet suspension balancing beam crane can be divided into the upper rotating electromagnet suspension balancing beam crane and the lower rotating electromagnet suspension balancing beam crane.
The electromagnet suspension balancing beam crane can be divided into two types based on the position of the plate (section steel) relative to crane’s main beam, Namely, the vertical to crane main beam type and the parallel to crane main beam.
Electromagnet suspension balancing beam crane can be divided into two types based on the connection form between the suspending beam and the trolley: rigid electromagnet suspension balancing beam crane and flexible electromagnet suspension balancing beam crane.
|
|
|
|
|
|
|
|
|
Electromagnet Suspension Balancing Beam Crane Category Summary |
|
|
|
|
|
|
|
|
|
|
|
|
|
|
|
|
|
|
|
|
|
|
|
|
|
|
|
|
|
|
|
|
|
|
|
|
|
|
|
|
|
|
|
|
|
|
|
|
|
|
|
|
|
|
|
|
|
|
|
|
|
|
|
|
|
Electromagnet Suspension Balancing Beam usage |
|
|
|
|
|
|
Connection form between balancing beam and trolley |
|
|
|
|
steel production placement direction |
|
|
|
|
|
|
|
|
|
|
|
|
|
|
|
|
|
|
|
|
|
|
|
|
|
|
|
|
|
|
|
|
|
|
|
|
|
|
|
|
|
|
general electromagnetic suspension balancing beam crane |
|
rotating electromagnet suspension balancing beam crane |
|
special electromagnet suspension balancing beam crane |
|
frigid electromagnet suspension balancing beam crane |
|
flexible electromagnet suspension balancing beam crane |
|
suspension balancing beam vertical to crane main beam |
|
suspension balancing beam parallels to crane main beam |
|
|
|
|
|
|
|
|
|
|
|
|
|
|
|
|
|
|
|
|
|
|
|
|
|
|
|
|
|
|
|
|
|
|
|
|
|
|
|
|
upper rotating electromagnet suspension balancing beam crane |
|
lower rotating electromagnet suspension balancing beam crane |
|
|
|
|
|
|
|
|
|
|
|
|
|
|
|
|
|
|
|
|
|
|
|
|
|
|
|
7.1.5 Coke Dry Quenching (CDQ) Coke Pot(Bucket/tank) Handling Crane
7.1.5.1 Usage
Dry quenching is an indispensable link in the coking process, It has the advantages of reducing dust pollution and emissions of CO and other harmful substances, improving coke strength, reducing blast furnace coking, and allowing recyclers to utilize and recover by-products. Dry coke quenching is a widely used metallurgy crane internationally .
The Coke Pot (Bucket/tank) Handling Crane is located on the running track above the dry quenching mast, it is one of the key equipment of the dry coke quenching system, Its main function is to transport the red coke pot to the dry quenching tank, and return the empty coke pot to the carrier vehicle. The carrier vehicle clamps the alignment device with the coke tank carrier vehicle, and the coke loading and loading device all have interlocking interactive process requirements. The automation level of the dry coke quenching system is very high, and the stable and reliable operation of the Coke Pot (Bucket/tank) Handling Crane is the basic guarantee for the normal operation of the dry coke quenching system.
7.1.5.2 Main Structure
Coke Pot(Bucket/tank) Handling Crane mainly composed by steel structure, lifting mechanism, travelling mechanism, spreader, coke pot (bucket/tank) cover, electrical equipment and maintenance cranes, etc.
 Coke Pot(Bucket tank) Handling Crane.WEBP)
7.2 Nonferrous metallurgy crane
7.2.1 Anode Baking Furnace Multifunctional Crane
Anode baking furnace multifunctional crane (FTM) refers to a specialized crane with a vacuum material conveying system, dust removal and cooling system, and anode carbon block tong device. It is a dedicated crane for the process line of anode carbon block baking, which is a specialized operating equipment for the anode carbon baking furnace. The entire machine mainly consists of tool trolley, crane bridge, long travel mechanism, crane operating mechanism, electric hoist and an electrical control system. The tool trolley is composed by suction and discharge system, tong device, trolley frame, a trolley travel mechanism and driver's cab. The entire crane adopts frequency conversion and PLC control.
7.2.1.1 Function
(1) feeding furnace: feed the unburned anode carbon block (green block) into the roasting furnace pit
(2) filling furnace: fill the granular coke in the material box into the gap between the baking furnace and the anode block, and cover the top
(3) Suction: Suck the furnace filling material into the silo
(4) Discharging: remove the fired anode block (cooked block) from the baking furnace and transport it to the conveyor belt or designated location
(5) Others assisting lifting work
7.2.1.2 Main Technical Data
(1) Suction capacity: 30t/h, 40t/h, 65t/h
(2) working class: A8
(3) Anode tong lifting capacity: 2X6t(Or clamp up the weight of 14 anode blocks)
(4) Filled coke state: Particle 0.8-5mm, temperature 450℃(600℃ in short time)
.WEBP)
7.2.2 Electrolytic Aluminum Multifunctional Crane (PTM)
The Electrolytic aluminum multifunctional crane is a key processing equipment for the production of large prebaked anode electrolytic aluminum, which can adapt to special environments such as high temperature, high current, strong magnetic field, dust and HF flue gas.
The unit is composed by crane long travel mechanism, bridge, tool trolley, aluminum production trolley, hydraulic pneumatic system, electric control system, etc. Its core is the tool trolley, which is composed by the trolley travel mechanism, trolley frame, tool rotating mechanism, shell breaking mechanism, anode replacement mechanism, slag removal mechanism, cutting mechanism, cab rotating mechanism, etc. The entire machine adopts frequency conversion and PLC control. The operation mode of the crane adopts the control room or remote control, and the two operation modes can cooperate with each other or be independently controlled. This unit has been widely used in the electrolytic aluminum industry and has been highly praised by users.
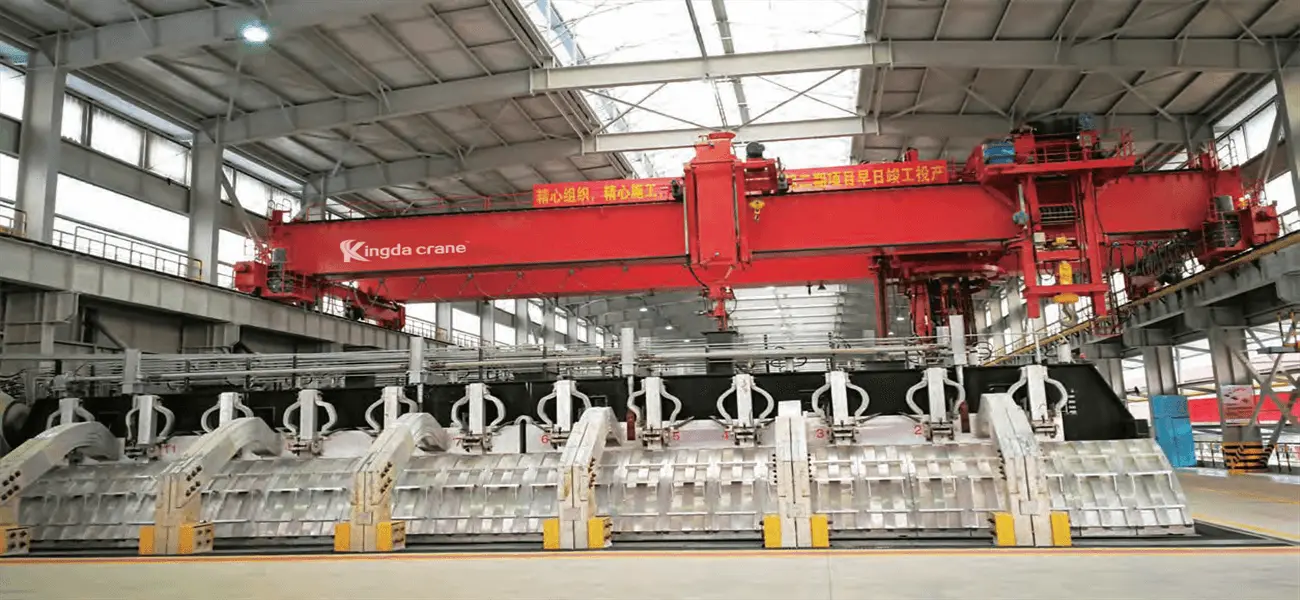
7.2.2.1 Function
At present, the rapid development of the aluminum industry has led to the widespread promotion of large prebaked anode electrolytic cells (180KA, 280KA, 300KA, 330KA, 400KA, 500KA), a high-level aluminum electrolysis multifunctional unit which to meet the production processing requirements of a large prebaked cell with multiple power inputs, the unit adopts advanced design methods and technologies such as lifting and engineering machinery, hydraulic and pneumatic transmission technology, and electronic technology, to complete following operating process:
1)Strike electrolyte crusting
2)replace the anode carbon block
3)add, cover aluminum oxide
4)aluminum Discharging
5) lift the anode bus-bar and lift other items during installation and maintenance of the electrolytic cell
6) remove slag
7) If necessary, fluoride salt feeding devices can also be configured
7.2.2.2 Operating Environment
The electrolysis workshop where the electrolytic aluminum multifunctional crane is located contains hydrogen fluoride corrosion gas, aluminum oxide, fluoride salt and carbon dust, as well as asphalt smoke, the unit operates 365 days a year, with a high load and frequent starts, and a large amount of work is carried out in high-temperature lava and strong magnetic field environments.
7.2.2.3 Main Technical Data
Items |
Unit |
Parameter |
Items |
Unit |
Parameter |
Span |
m |
|
material box volume |
m3 |
<4 |
working level |
|
A6-A8 |
aluminum discharging trolley weight |
t |
10~16(25) |
long travel speed |
m/min |
6~60 |
hoist weight/ set |
t |
8~16 |
main trolley travel speed |
m/min |
4~30 |
hydraulic system rated working pressure |
Mpa |
22 |
anode extraction mechanism Maximum pulling force |
kN |
70 |
hydraulic system rated flow rate |
L/min |
38 |
Anode fixture opening and closing mechanism clamping torque |
N.m |
250~350 |
air compressor rated working pressure |
Mpa |
0.75 |
hitting head impact absorption energy |
J |
≥85 |
air compressor rated air flow rate |
m3/min |
7 |
hitting head impact frequency |
Hz |
20 |
total Installed capacity |
kW |
150~250 |
7.2.3 Anode Carbon Block Stacking Crane (ASC)
7.2.3.1 Usage
The anode carbon block stacking crane is a specialized equipment for handling and stacking anode carbon blocks, mainly used in the carbon block warehouse of large prebaked anode electrolytic aluminum plants. The raw carbon blocks produced from the vibration-forming section must first be transported to the anode baking workshop for baking. The baked mature carbon blocks are then transported to the carbon block warehouse and then assembled in the anode assembling workshop. The anode carbon block stacking crane is responsible for the transportation of carbon blocks in this process.
According to the different settings of the marshalling machine, it is generally divided into two types: longitudinal conveying and transverse conveying. The longitudinal conveying transported carbon blocks are equipped with a fixture device consisting of 10-11 pneumatic fixtures, which supports a group of 10-11 vertically arranged carbon blocks for transportation, using an electric hoist to remove waste blocks from longitudinal arranged carbon blocks group and insert qualified carbon blocks. The electric hoist can also complete the lifting operation of sporadic materials in the workshop.
When conveying horizontally(longitudinal),the horizontally transported carbon blocks consist of a fixture device consisting of 21 pneumatic fixtures, which can hold 21 carbon blocks at once and stack and transport 21 sets of longitudinal arranged carbon blocks at once.
The carbon block stack that has been transverse transported, the stability of each pile is poor, and often there are employees cleaning between the piles. In the event of a coal block toppling, the escape route for employees is relatively long, Personal injury and death accidents are prone to occur. The charcoal block toppling will be like a domino, Push down few blocks one time, a large area of carbon stamps in the workshop will be pushed down.
And the stacking completed by horizontal transportation, the stability of each pile is relatively good, and the carbon blocks at both ends are relatively easy to topple, only a few pieces. When pedestrians walk in the vicinity, even if a block falls, it is easy to avoid danger and fully utilize the effective workshop area.
7.2.3.1 Structure and Characteristics
Anode carbon Block stacking crane (ASC) is divided into two kinds: Split sleeve type and hinge joint type, it is composed by electrical control system, lifting mechanism, fixture device, crane traveling mechanism, bridge, pneumatic system, electric hoist, etc.
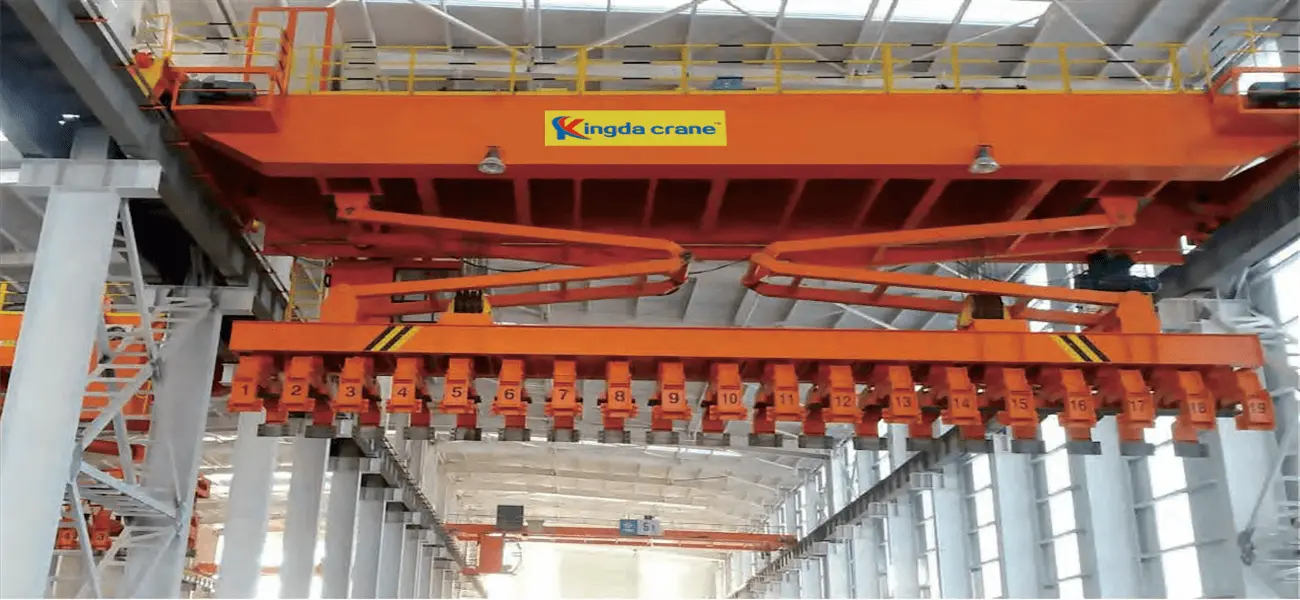
7.2.4 Electrolytic Multifunctional Copper Crane
The combined electrolytic copper multifunctional crane is Kingda crane’s intelligent product, which is a specialized crane developed and manufactured according to the production process requirements of electrolytic copper. This crane is suitable for special working environments such as high humidity, corrosion, and metal dust. High standard design, manufacturing, and assembly ensure the safe and reliable operation of various mechanisms; Its highly intelligent automation control system and lifting appliances ‘s effective integration have unparalleled advantages.
7.2.4.1 usage
The electrolytic copper crane is a specialized lifting equipment for the electrolytic copper production process, the dedicated lifting tool designed for the placement position and form of the cathode and anode plates can efficiently load or lift the cathode and anode plates into or out of the electrolytic cell.
Electrolytic copper crane main workflow:
1) Take the anode plate from the preparing rack and load it into electrolytic cell;
2) Take the cathode plate from the preparing rack and load it into electrolytic cell;
3) After electrolysis, remove the cathode copper and collect acid liquor from acid drip tray
4) Retrieve acid drip tray and place cathode copper in the detergent group
5) Remove anode residue and collect acid solution in a drip tray
6) Retrieve the acid drip tray and place the anode residue in detergent group
7 Cycle the above process. Usually, installing one anode corresponds to installing three cathodes
Electrolytic copper crane auxiliary work:
1) Electric hoist lifts residual electrode after anode electrolysis
2) Electric hoist lifting single pole plate
3) Electric hoist completes other auxiliary lifting work
7.2.4.2 Main technical parameter
Operating environment: Wet, with acid mist, temperature 25-45 ℃;
Lifting capacity: main lifting≥22t;
Lifting speed: main hook:1.2!12m/min;
Whole crane working class: A6;
Long travel speed: 8.5~85m/min
Cross travel speed: 4~40m/min.
7.3 Hot Working crane
7.3.1 Forging Crane
Forging cranes are one of the main equipment in large-scale forging manufacturing processes. The forging crane is one of the main equipment in large-scale forging manufacturing processes, which mainly applies pressure to metal billets through a forging press to produce plastic deformation and obtain products with certain mechanical properties, shape, and size. Forging cranes are used for lifting and flipping metal billets, as well as to avoid damage to mechanisms or structural components due to impact loads by setting buffer devices. Forging cranes mainly have two structural forms: double beam - double track-single trolley and three beam -four track- double trolley. The structural form of forging cranes is closely related to the layout of forging workshops and hydraulic presses. The composition of a forging crane includes an electric control system, main (auxiliary) trolley, crane travelling mechanism, bridge, lifting tool and tipping device.
7.3.2 Quenching Crane
Quenching crane is an overhead crane used for vertical well quenching heat treatment process, and has the function of rapid descent and emergency brake release in case of accident. It is a special lifting equipment configured in the heat treatment plant, usually in the form of double beam single trolley structure. The main functions of the quenching crane are: immerse quickly the heated high-temperature hot work piece into the quenching pool (quenching well) to complete the quenching heat treatment work.
7.3.2.1 Structure and Characteristics
To ensure that the work piece can achieve ideal heat treatment performance while reducing the probability of liquid level lighting fire in the quenching pool (quenching well), Usually, the quenching crane is required to quickly submerge the work piece below the quenching liquid level. This characteristic of the quenching process determines that the lifting mechanism of the quenching crane must have the function of rapid descent.
To avoid during the quenching process, due to unexpected circumstances, the work piece could not be quickly placed in the quenching pool (quenching well), leading to a fire, therefore, the lifting mechanism with quenching function must be equipped with an emergency release function, which can quickly put the work piece into the quenching pool (quenching well) in case of unexpected situations, to avoid the occurrence of malignant events.
The supplier of lifting solution
Kingda Crane